激光高效切割电动汽车整组管件 电动汽车的大趋势要求汽车零部件的生产有新的解决方案。弯管、液压成形管和管状框架正成为电动汽车设计中的关键部件,但这些部件的加工对设备供应商提出了特殊的挑战。由于安全性的要求,管状框架的生产是其中一个挑战。管状框架生产是指将组成管状框架的所有管子以一个批次(或批次号为1)进行加工,然后焊装(或组装)成一个管状框架。如果采用传统激光切割设备,由于要切割的不同管子的数量多,因此需要使用大量夹具。对于不同尺寸、形状和切割任务的管子切割,需要高度灵活的激光加工解决方案。
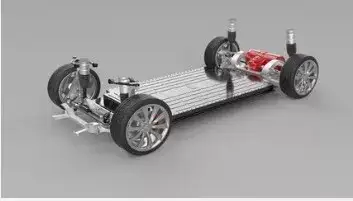
(电动汽车底盘)本文阐述了一种应对挑战的基于机器人的管件切割解决方案,展示基于机器人的3D激光切割系统通过采用最先进的技术、零夹具的方案实现灵活性和切割精度的要求。 一、电动汽车管状框架 这里的案例着重阐述了一种新型电动汽车管状框架的生产。该框架的功能是承载电机和支撑部件,并隔离振动。对管状框架的要求特别高,因为它必须能够承受750牛米以上的电机扭矩,以及与内燃机相比约150公斤的额外重量。此外,这个管状框架还是电动汽车碰撞结构的一部分。 这种框架由三到十根单个管件组成。这些管件是弯曲的三维形状,激光切割后焊接成一个完整的框架。由于安全和可追溯性方面的考虑,这些管状框架是在一个批次生产。这意味着,一个管状框架所需的所有单独的管件都是在一个批次中顺序完成生产的,然后焊接成一个成品框架。 除了可追溯性,这种工艺有一个优势:汽车制造商不需要在生产的中间环节存储单个管子。只生产成品框架。 为了进一步提高灵活性,在生产线上以随机的产品顺序生产几种不同类型的管状框架,而不需要更换夹具。因此,根据要求的变化可以快速地调整生产。 这种非常灵活的单批生产对生产设备的要求特别高。下面将重点讨论通过激光加工单元实现这些特别的要求。
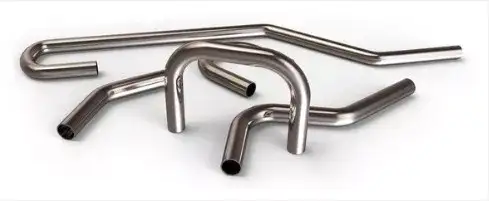
(单个弯管)二、新概念的形成 据测算,使用传统的激光加工方法将需要4台龙门式激光切割机来实现单批生产。相应的设置时间、高昂的物流成本和额外的空间要求使得这种方法不可行。 为了取代传统龙门式激光切割机,必须开发出一种新的高度柔性激光切割概念(见图2),其基础是现有的内导光(beam-in-motion,BIM)概念,即激光光束在切割机器人内部传导。由于没有传输光纤,激光切割头非常轻,因此切割机器人的动态性能更高而且运动非常精确。由于切割头上没有活动的传输光纤,也没有笨重的光纤连接器,使得复杂管件的可及性得到了改善。 考虑用搬运机器人取代复杂的激光切割夹具,将“内部材料输送”和“呈现在内导光切割机器人面前”这两个必要的工作步骤合并到了一个功能单元里面。 最后一个组件-图像处理被引入以满足新的生产需求。图像处理解决方案能够确定管子的生产偏差,并补偿公差。
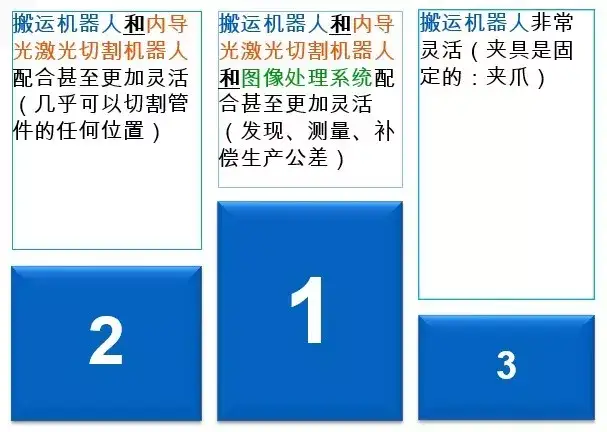
(业纳新概念的优点)三、高度灵活的激光切割系统 概念开发完成后,建立了具有两条加工线的激光加工单元。每条加工线由一个激光切割机器人和两个搬运机器人组成(图3),在激光加工单元的中心是一个废料传送带,它将切割废料运送出激光加工单元。来料通过激光安全室被输送到位于激光加工单元一侧的托盘上。在另一面,加工后的材料被放置在另一个托盘上,并通过输出室运出。其他部件,如激光源、冷水机和控制柜,则放置在机器上方的夹层上。这也节省了占地空间。
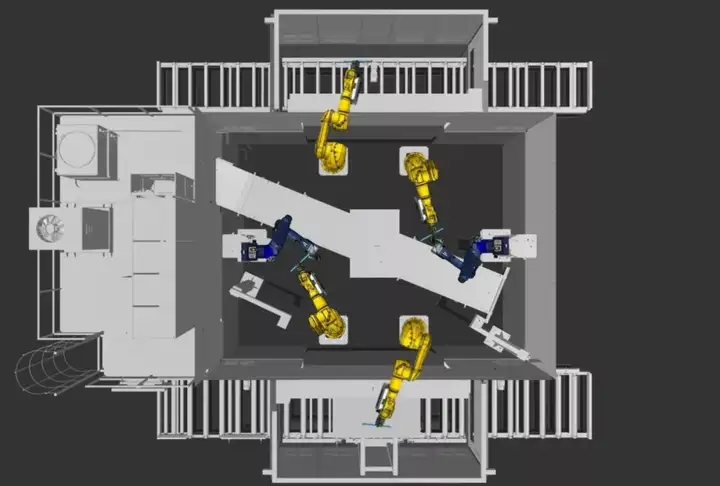
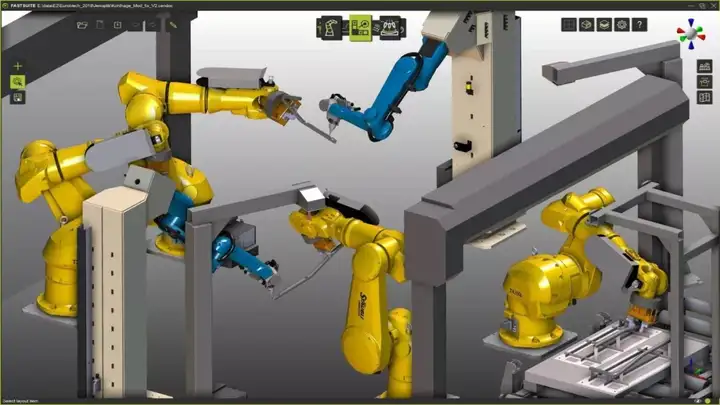
JENOPTIK-VOTAN®BIM激光加工单元鸟瞰图(a)和3D图像系统(b)激光切割机器人(蓝色)和搬运机器人(黄色)四、工艺流程图 该工艺按照物流顺序进行(见图5),首先将载有未加工管件的入料托盘送入机器。图像处理单元1 (IP1)检查哪个托盘已经加载、哪个程序应该被调用。此外,还检查了管件位置的当前外形。 图像处理单元2 (IP2)检查管件的正确位置,并将偏差作为偏移量传递给搬运机器人。这样可以确保管件始终被正确地夹紧。测量未加工管件的长度,以确保它们不超过最大允许长度。如果管件尺寸超过最大值,程序将不会启动,以避免损坏设备。 一旦这些检查完成,搬运机器人1 (HR1)将管件从托盘中取出,并将其放在安装在加工区内的图像处理单元3 (IP3)前面,IP3识别搬运机器人夹爪中的管件。将图像与存储的参考形状进行比较。任何偏离基准形状的偏差都作为偏移量传递给搬运机器人,使其将管件保持在内导光激光切割机器人前方的正确位置。如果当前管形超出允许的公差范围,则停止进一步加工。 下一步,搬运机器人1 (HR1)将管件呈现给内导光(BIM)激光切割机器人,开始切割管件的第一部分。这部分切割完成后,考虑到之前从图像处理中确定的偏移量,管件被移交给搬运机器人2 (HR2)。然后,内导光(BIM)激光切割机器人切割管件的第二部分。切割的同时,搬运机器人1抓取下一根管件,图像处理执行所有判断步骤。因此,整个系统能够达到高质量、高效率的量产要求。 激光切割完成后,搬运机器人2 (HR2)将成品管件放到输出托盘的指定位置。如果托盘上的所有管件全部切割完成,则激光安全室关闭。下一批开始加工时,托盘就可以运输出去。 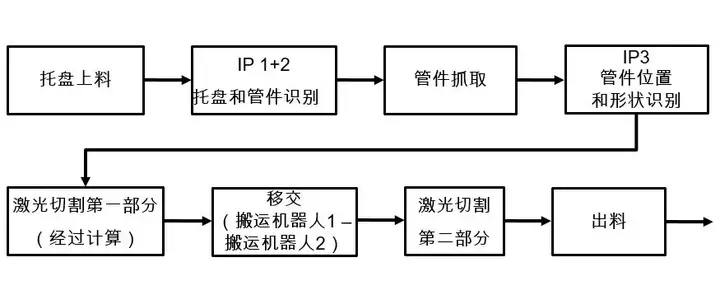 五、总结 通过使用三种灵活的元件(搬运机器人、内导光(BIM)激光切割机器人和智能图像处理解决方案),建立了一种高度灵活的、免夹具的激光切割解决方案,可满足单批管状框架生产所需。通过重复性试验验证了所要求的+/- 0.4毫米的位置精度和+/- 0.2毫米的几何公差都能满足。 因此,无需更换夹具和较长的安装时间,就可以切换生产不同的管状框架。此外,在弯管过程中不可避免的生产公差可以得到补偿。如果生产公差超过允许范围,激光系统将报告这些偏差并停止进一步加工。因此,它提供了一个对每一个管件的额外的实时质量检查,这是独立于加工周期的。 目前,第一套系统已经交付给最终用户进行生产。有了这种新颖的激光切割系统,汽车行业就拥有了满足高度灵活的电动汽车生产要求的先进工具。
|